Products List
- Welding Lathe
- Automated Welding Center
- Resistance Welding Equipment
- Welding Auxiliary Equipment
- Robotic Welding System
- Household Appliance Welding Equipment
- Strips Welding Line in Metallurgical Industry
- Welding Production Line for Auto Parts
- Shock Absorber Seam Welding Machine
- Fuel Tank Welding Producion Line
- Welding Production Line for Aluminum Alloy Fuel Tank
- Welding Production Line for Automobile Gas Storage Tank
- Welding Production Line for Transmission Shaft
- Car Rear Axle Welding Line
- Welding Production Line for SUV and Pickup Drive Axle
- Trailer Axle Welding Production Line
- Truck Drive Axle Welding Line
- Welding Production Line for Heavy Vehicles Drive Rear Axle
- Automatic Welding Line for Car Rear Axle Assembly
Welding Production Line for Heavy Vehicles Drive Rear Axle
Description
Welding production line can be used for welding drive rear axle of heavy vehicles, especially for heavy duty automobiles. It mainly consists of eleven process equipment. They are plasma cutting robotic welding system for rear axle, circumferential automatic welding equipment for rear axle and half shell oil drain plug, assemble welder and straight seam or Y seam automatic welding machine for middle rear half shell, precise CNC plasma cutting machine for rear axle, reinforcing ring assemble spot positioning and automatic welding machine for rear axle, rear cover assemble spot positioning and automatic welder for rear axle, press fitting and flange spot positioning tooling equipment, circumferential welding equipment for middle part of axle and axle shaft tube, assemble contact welding machine for assemble axle and accessories (plate spring seat and racket, etc.) and hydraulic straightening machine for assemble axle.
Welding Production Line for Heavy Vehicles Drive Rear Axle
1. Robotic Plasma Cutting Machine for Rear Axle
1) It adopts robot to process half shell bevel cutting.
2) It employs precise plasma cutting process with high cutting accuracy.
3) Double-station and double-robot working mode makes it work with high efficiency.
4) In welding production line, it takes the advantage of full enclosed structure and multi-channel air draft device to guarantee applicable working condition.
Suitable Work Piece | Heavy Axle Shell |
Processing Method | Plasma Cutting |
Processing Equipment | Robot |
Station Condition | Double Station |
Production Rhythm | 25 pcs/min |
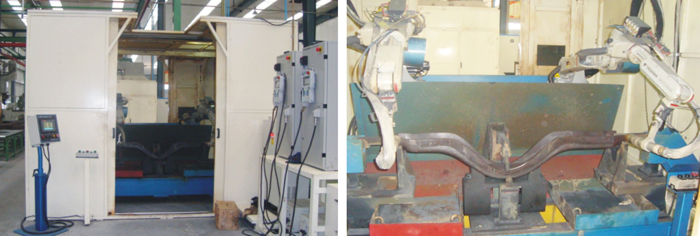
2. Circumferential Automatic Welding Machine for Rear Axle and Half Shell Oil Drain Plug
(1) This automatic welding equipment is mainly used to realize circumferential CO2 automatic welding process.
(2) In welding production line, itmakes use of half shell positioning fixture for clamping and welding torch rotating process.
(3) Open type and enclosed type protective structure are optional.
(4) Consumable electrode gas protection welding method is adopted.
3. Welding Machine for Middle Part of Rear Half Shell
Method One
Rear axle and half shell assembly tooling (manual spot welding) adopts special pneumatic self-centering fixture for middle clamping and positioning. Besides, it makes use of electric rotating structure and manual welding method.
Method Two
In welding production line, it employs double-robot double-station assemble spot fixing backing welding workstation. It utilizes electric rotating structure and special pneumatic self-centering fixture for middle clamping and positioning. With double-robot double-station layout and full enclosed structure, it features high efficiency and stable welding quality.
4. Straight Seam or Y Seam Automatic Welding Equipment for Middle Rear Half Shell
Method One
Longitudinal Seam Automatic Welding Machine for Middle Rear Axle
In welding production line, it adopts hydraulic clamp, submerged-arc welding and numerical control profile welding method. Such automatic welding equipment can carry out high-frequency induction heating.
Method Two
It makes use of pneumatic clamp, submerged-arc welding and numerical welding method. Flux recovery device is optional.
Method Three
Longitudinal Twin-Wire MIG Robot Welding Workstation for Middle Rear Axle
In welding production line, such automatic welding equipment employs robot welding method and twin-wire MIG welding process for this workstation. And double-station layout, full enclosed mechanism and special pneumatic clamp are mounted on this Robotic Welding System.
Method Four
Longitudinal SeamCO2/MAG Welder
In welding production line, it makes use of special welding mode and MAG welding process with the work piece fixed.
Double Robot Double Station Y Seam MAG Welding Workstation for Axle
Special MAG Straight Welding Machine with Two Torches for Axle
5. Precise CNC Plasma Cutting Machine for Rear Axle Pipa Shaped Bore and Gap
In welding production line, it takes the advantage of clamp for fixing the work pieces and adopts precise plasma cutting power source with three side surrounded structure. The work pieces can rotate automatically. And the welding torch conduct automatic CNC cutting to pipa shaped bore and gap in middle axle.
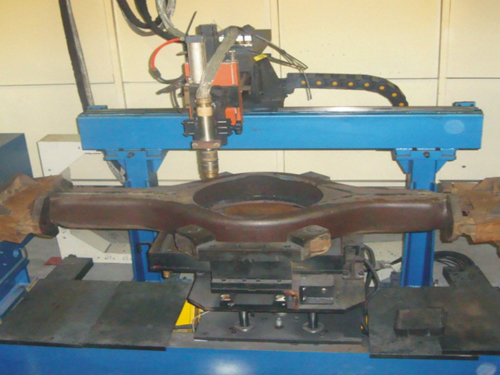
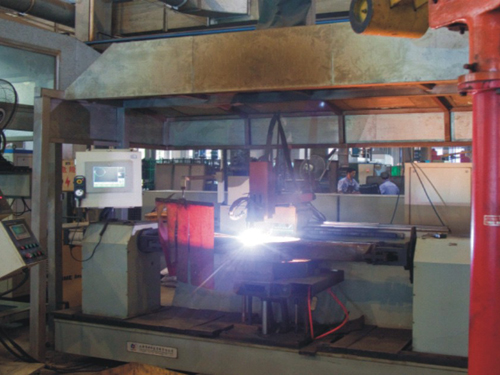
6. Reinforcing Ring Assemble Spot Positioning and Automatic Welding Machine for Rear Axle
Method One
Reinforcing Ring Circumferential Automatic Welding Machine for Rear Axle (Common Control Mode\Numerical Control Mode)
Special Reinforced Ring Numerical Control Profile Circumferential Welding Mode (Vertical Structure)
Reinforced Ring Circumferential Welding Mode (Round Reinforced Ring Circumferential Welding Mode)
Special Reinforced Ring Numerical Control Profile Circumferential Welding Mode (Horizontal Structure)
Reinforced Ring Assemble Spot Positioning for Rear Axle
Method Two
Special Reinforced Ring and Circumferential Automatic Welding Machine for Middle Rear Axle
In welding production line, it employs backing self centering mechanism, pneumatic mode and full-length welding without spot positioning method.
Clamping State Diagram
Method Three
Reinforced Ring Robot Double-Station Welding Workstation for Middle Rear Axle
In welding production line, it utilizes single robot, double-station and enclosed mechanism, pneumatic self-centering fixture for positioning, full-length welding with robot and automatic tracking mode. Besides, special pneumatic clamp is adopted to fix the work piece. This welding workstation fits to continuous production.
7. Assemble Spot Positioning Automatic Welding Equipment for Rear Cover of Rear Axle
Method One
Rear Cover Assemble Spot Positioning Tooling and Reinforced Ring Circumferential Welding Machine
Rear Cover Circumferential Welding Mode (Round Rear Cover Welding Mode)
Rear Cover Assemble Spot Positioning for Middle Rear Axle
Special Rear Cover Numerical Control Profile Circumferential Welding Mode (Vertical Mode)
Special Rear Cover Numerical Control Profile Circumferential Welding Mode (Horizontal Type)
Method Two
Robot Double-Station Welding Workstation for Rear Cover of Middle Rear Axle
In welding production line, it makes used of single robot, double-station and enclosed mechanism, pneumatic self-centering fixture for positioning, full-length welding with robot and automatic tracking mode. Besides, special pneumatic clamp is adopted to fix the work piece. This welding workstation is suitable for continuous production.
Method Three
Inner Circumferential Robot Double-Station Welding Workstation for Rear Cover of Middle Rear Axle
In welding production line, it adopts single robot, double-station full enclosed mechanism, and special welding torch, pneumatic backing self centering structure and full-length welding method.
8. Press Fitting and Flange Spot Positioning Equipment for Middle Axle and Axle Shaft Tube
Method One
Rear Cover Spot Positioning Equipment and Reinforced Ring Seam Welding Machine
Hydraulic Press Fitting Mode
Pneumatic Press Fitting Mode
9. Circumferential Welding Equipment for Middle Part of Axle and Axle Shaft Tube
Method One
In welding production line, it can carry out flame preheating and welding with two torches for multilayer multi-channel. Besides, this machine adopts horizontal welding mode.
Method Two
Double-robot circumferential welding workstation for middle axle and axle shaft sleeve makes use of double torches for multi-channel welding.
⑴ Single-Station Double Robot Welding Workstation;
⑵ Seam Welding for Spindle Head, Automatic Welding for Flange Plate
⑶ Rotary Work Piece and Robot Linkage, Testing and Tracking Welding Position
⑷ Full-Enclosed Structure, Good Ventilation Effect
Method Three: Special Circumferential Welding Workstation with Four Torches for Middle Axle and Flange Plate
Method Four: Special Circumferential Welder with Six Torches for Middle Axle, Axle Tube and Flange Plate
10. Assemble Contact Welding Machine for Assemble Axle and Accessories (Plate Spring Seat and Racket, etc.)
In welding production line, it makes use of electric rotating structure mode, hydraulic fixture for clamping and manual spot welding for fixation.
Robotic double-station welding workstation for axle and big bracket (plate spring seat) employs special hydraulic clamp, electric rotating mode and external drive shaft.
Single Robot Double Station Welding Workstation for Axle Accessories (Splayed Double Station Layout Mode)
Single Robot Double Station Welding Workstation for Axle Accessories (H Shapes Double Station Layout Mode)
11. Hydraulic Straightening Machine For Assemble Axle
This straightening equipment includes the following two modes:
(1)Transmission Line Gantry Hydraulic Host Mode
(2) Single-Column Hydraulic Host Mode
TallKee Technology is a professional supplier of welding production line for heavy vehicles drive rear axle in China. We are engaged in providing automatic welding equipment, seam tracker, wire feeder and other auxiliary machines which feature large productivity, high efficiency, cost effectiveness and environmental protection. For detailed information about welding production line, please enter our website or contact us directly.
Related Products
- Roller Cladding MachineRoller Cladding Machine can be used to resurfacing weld roller, rotary surfaces and other alloy materials with wear-resistance, anti corrosion and high temperature. Besides, such buildup welding equipment is capable of repairing the frayed roller. It is widely applied in iron and steel manufacture. ...